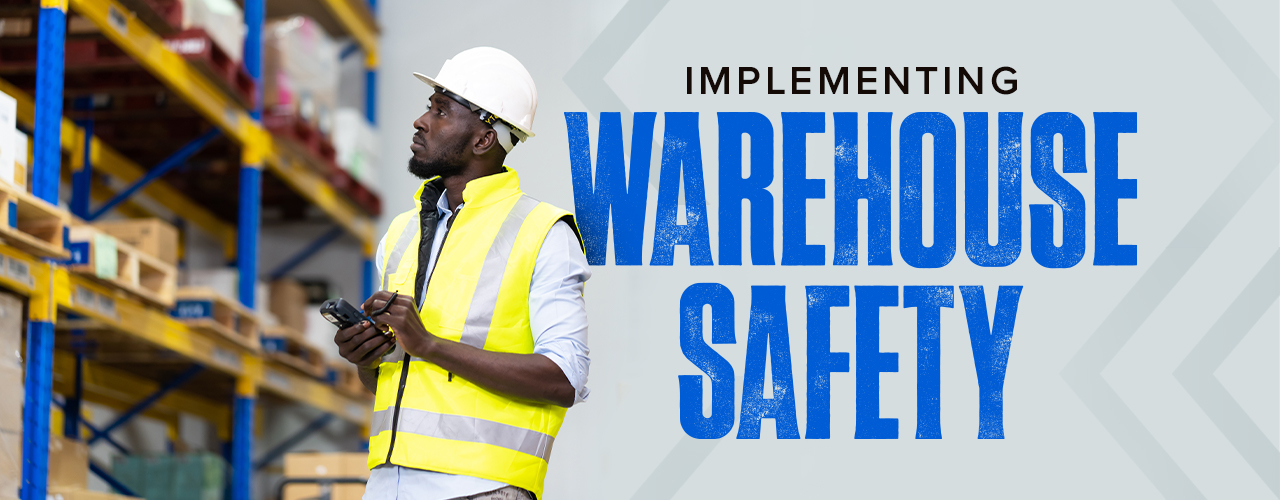
If you are opening a warehouse, getting every single detail right can seem daunting, and knowing what to prioritize is even more challenging. When it comes to the safety of your employees, we’ll make it simple for you: before employing your warehouse staff, you need to strategize and implement warehouse safety procedures around your facility.
Once you've hired your employees, educate them on popular safety acronyms so they can evaluate risks and respond to emergencies. Below we have outlined the various warehouse safety standards set by the Occupational Safety and Health Administration (OSHA) so you can be certain that your warehouse safety is good to go.
OSHA’s 10 Most Commonly Cited Warehouse Safety Hazards
If OSHA finds a safety violation in your warehouse where safety standards are not being met, they will issue a costly citation. Below is a list of OSHA’s most common warehouse citations:
- Forklifts
- Hazard communication
- Electrical, wiring methods
- Electrical, system design
- Guarding floor & wall openings and holes
- Exits
- Mechanical power transmission
- Respiratory protection
- Lockout/tagout
- Portable fire extinguishers
Warehouse Safety Topics
To reduce the probability of being cited for one of OSHA’s most common citations, follow OSHA’s guidelines list below (found in their Warehousing Safety Brochure) on reducing hazards in specific areas of the warehouse:
1. Forklift Safety
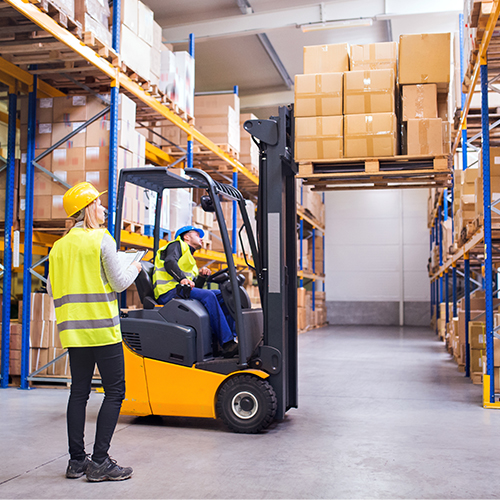
Understanding and training your employees on proper forklift safety is extremely important. According to OSHA, about 100 employees are killed and 95,000 are injured every year while operating forklifts. In fact, it is best to avoid working at heights unless absolutely necessary, especially when considering forklift and even ladder safety.
Apply the same rules as driving a car to driving a forklift such as paying attention to speed limits, wearing a seatbelt, and watching where you are driving. If anything, more caution should be taken while operating a forklift as workers walk freely throughout the warehouse.
Below are a few solutions to avoiding forklift hazards according to OSHA:
- Ensure that all employees can operate forklifts safely by providing proper training, evaluation, and certifications for all operators
- Create safe clearances for forklifts in aisles and loading docks, and prevent noxious gases from forming by ventilating parked forklift areas
- Maintain the quality and upkeep of a forklift by checking for hazards before driving and examining hazardous conditions
2. Loading Dock Safety
An elevated surface can create more hazards than one might think. Products falling on employees, improper use of equipment, and being unaware of the dock’s edge are just a few problems that can happen in the loading dock area.
With that, it's important that traffic control plans are developed to avoid collisions. Loading dock edges should be properly lit and marked with visual warnings as helpful visuals for drivers and employees. Guard rails should also be installed for further protection for employees, to discourage jumping, and other poor ergonomics or horseplay. Another consideration is proper ventilation to prevent noxious fumes from forming.
Below are OSHA’s recommendations on avoiding potential loading dock hazards:
- Make sure to secure the dock plates and check to see if they can safely support the load
- Dock edges should be clear and have signs that provide visual warnings
3. Conveyor Safety
Because conveyor belts are ongoing machines, they pose a wide variety of potential hazards to your employees. Risks like clothing or jewelry getting caught, standing and falling off the conveyors, and items getting stuck in the belt can pose very unsafe threats for your employees.
Make sure employees are wearing mandated safety uniforms to reduce the risk of clothing getting caught, while training them on the dangers of standing, sitting, and walking on the moving belt. It's also important to note that if items are caught in the belt, a lockout system is initiated instead of trying to resolve the problem while the conveyor belt is still operating.
From being caught in pinch points to products falling off the belt, find out how to deflect common hazards with conveyor safety solutions as outlined by OSHA:
- Identify pinch points and ensure they are adequately guarded
- Create systems that lockout conveyors and train employees in these procedures
4. Material Storage Safety
Properly stacking and storing materials using material handling equipment is imperative when working with tall shelving units in your warehouse. Keep in mind proper box and pallet stacking patterns to maximize space and secure storage. When stored improperly, the materials may fall and injure workers. Properly storing equipment, such as ladders, also prevents workplace accidents and prolongs the life of the equipment. Because of this, you'll want to supply your workers with PPE such as thick gloves to avoid sharp edges and steel-toed safety boots to prevent foot injuries. Other great products to supply your employees with are handles or holders that can be attached to heavier loads as it makes it easier to maneuver the load and reduce any pinched fingers.
To avoid these maladies, follow OSHA’s safety guidelines for material storage:
- Boxes need to be stacked straight and evenly, and the heavier loads should be stacked on the lower or middle shelves
- Aisles and passageways need to be clear of any objects
5. Manual Lifting Safety
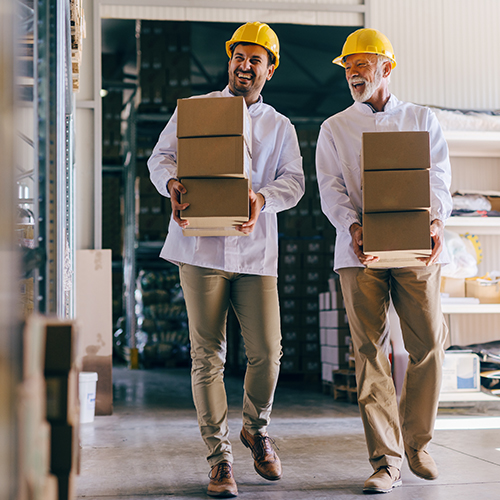
Protecting your employees’ well-being is paramount to being a good employer and keeping your workers employed. During a laborious job, your employees can sustain short- or long-term injuries from improper lifting or overexertion. Luckily, there are a lot of ways to eliminate this!
Before onboarding employees, focus on the design and function of the work environment to fit employees' physical requirements, such as safety devices, lighting, tools, and other aspects of the various workstations. Checking these ergonomics and structuring them with employees in mind reduces repetitive motion injuries and other stressors. In short, you need to make the job as easy as possible for them to carry out.
OSHA’s solutions on avoiding improper manual lifting and handling should be instilled into your daily operations:
- Mandate training for general ergonomics and encourage employees to help/ask for help when a product is too heavy
- Eliminate or minimize the need for lifting by acquiring well-designed engineering techniques
6. Hazard Communication Standard
Hazardous chemicals can be common in certain types of warehouses. The Hazard Communication Standard (HAZCOM) is a requirement by OSHA for employers in the United States to disclose hazardous substances in a workplace. Being cautious of where these are present in your facility and knowing how to take action when spills of hazardous materials occur is extremely important for your employees’ safety.
Below are solutions from OSHA for dealing with hazardous materials and how to prevent them in the first place:
- All chemicals in the warehouse should have Material Safety Data Sheet (MSDS) with instructions on how to handle the chemicals
- Write out a spill control plan and have spill cleanup kits present anywhere that the chemicals are stored
- Train each employee about the hazards of the chemicals being stored, how to properly wear their PPE, and how to clean up the spills
7. Battery Charging Station Safety
While charging stations are important for energizing your electric equipment, they can also pose dangerous threats if not treated with caution. These stations house powerful fueling operations such as gasoline, batteries, and liquid petroleum gas. Hazards like fires and explosions are possible if guidelines and general safety aren’t followed around these stations.
Taking preventative measures to avoid hazards in your charging station are outlined in OSHA’s guidebook as follows:
- Forbid smoking or any open flames in charging station areas and keep fresh air flowing or adequate ventilation to prevent noxious gases from forming
- Follow procedures for refueling gas or propane forklifts and provide readily available and fully charged fire extinguishers
- Install an eyewash station and safety shower for employees to use in case of exposure to battery acids
8. Ergonomics Safety
Along with improper manual lifting, employees can also injure themselves from continuously performing repetitive motions or injure themselves from poor design of the operation. While there is training that can be done to show your employees how to perform their tasks safely, there are also machines and tools to look into for additional security.
Some machines to check out are tilters, tilted pick trays, and back saver lifts. All of these heavily reduce repetitive motions like bending and twisting. Tilters position boxes so the contents are easier to access instead of bending in, reaching, and pulling contents out over and over again. Tilted pick trays help workers see the items that are higher up on the pallet track so they can pick the boxes with confidence instead of scaling beams or reaching into boxes blindly and wasting time. Finally, back saver lifts are perfect for your employees who lift, stack, and assemble all day long. These machines help with positioning and pallet picking!
To keep your employees safe and healthy both short and long term, follow OSHA’s solutions for proper ergonomics in the warehouse:
- Eliminate lifts from floor to shoulder height by raising the shelf or bin
- Educate employees to lift with their legs and keep their backs in natural positions
- Encourage employees to test the load before manually lifting to ensure they can handle the weight and size and decide which lifting method they should use
Back to Top
Additional OSHA Safety Topics
To further strengthen your warehouse safety standards, we have outlined additional advice and solutions that you can implement in your facility:
1. Provide Appropriate PPE

According to OSHA’s PPE Brochure, employers are responsible for evaluating their warehouses and assessing what PPE is needed to keep employees safe. Here are the steps to follow to decide what PPE is necessary for your business:
- Performing a “hazard assessment” of the facility. To first decide what safety measures need to be taken, it's important to identify the hazards around your facility. A hazard assessment is just that. A hazard assessment identifies both physical hazards (such as moving objects, intense lighting, electrical connections, etc.) and health hazards (such as excessive dust and exposure to harmful chemicals or radiation).
- Identifying and providing appropriate PPE for employees. After the hazard assessment, analyze the data to determine the proper PPE needed at the warehouse. Familiarize yourself with the different types of PPE available as well as the different levels of protection. You can never go wrong with selecting PPE that will provide more protection than the minimum required so you can keep your employees safe from hazards!
- Training employees in the use and care of the PPE. Demonstrate to each employee how to properly wear and use PPE before they work. If you notice that an employee who has received training is not practicing the proper use of PPE, that employee needs to be trained again. You should also retrain employees if the warehouse changes or new PPE needs to be used to complete tasks.
- Maintaining PPE, including replacing worn or damaged PPE. According to OSHA's PPE Handout, employers must provide and pay for PPE as well as replace PPE as needed to keep workers safe. Encourage your employees to talk to management immediately when PPE is damaged, and keep a supply of extra PPE on hand to quickly remedy these situations.
- Periodically reviewing, updating, and evaluating the effectiveness of the PPE program. Schedule regular, periodic times to reassess your facility for changes in equipment use, operating procedures, and other conditions that may affect occupational hazards. It’s also recommended that you review injury or illness records to find patterns that could be addressed, as well as evaluate PPE to assess its current condition.
2. Mandatory Signage
OSHA’s signage guidelines inform employers of the types of warehouse signage that are needed, where they should be placed around the facility, and how to properly display them.
There are many different categories that your safety signs will be needed for: notice, general safety, admittance, fire safety, and non-hazard. Each sign present should have one of three levels of classification: caution, warning, or danger.
- Caution Signs: Potentially hazardous area that may cause minor injuries.
- Warning Signs: Area that requires special attention and may have unexpected hazards.
- Danger Signs: The most hazardous area that could have life-threatening conditions.
3. Fire Prevention Plan
Create a fire prevention plan to eliminate any potential risk for fires in your warehouse. Follow OSHA’s fire prevention plan requirements for a list of what to include in your plan, including fire prevention supplies you may need. This plan should be written out and kept in the workplace, making it readily available for an employee to review at any time. As an employer, you are also required to inform each employee about fire hazards they are exposed to and review the fire prevention plan with them as well.
4. Emergency Action Plan
An emergency action plan (EAP) is a written document that outlines the actions that should be taken by employers and employees during a workplace emergency. Develop an EAP according to OSHA’s standards, and train your employees with the EAP plan and update as needed.
For a more detailed list of these requirements, check out OSHA’s EAP minimum requirements page.
5. Standard Operating Procedure (SOP)
A Standard Operating Procedure (SOP) is a list of step-by-step instructions outlined by an employer to assist workers with routine tasks. SOP’s are essential for businesses as they reduce failures of complying with industry regulations and reduce miscommunication. SOP’s promote efficiency, performance quality, and consistent output results.
Back to TopBesides costing potentially thousands to ten thousands worth in damages, turnover, loss of sales, and lawsuits, keeping your employees safe for the simple matter of maintaining their quality of life is the number one factor of why warehouse safety matters. According to OSHA, the fatal injury rate for the warehousing industry is higher than the national average for all industries, so it is imperative to follow the warehouse safety standards set by OSHA.