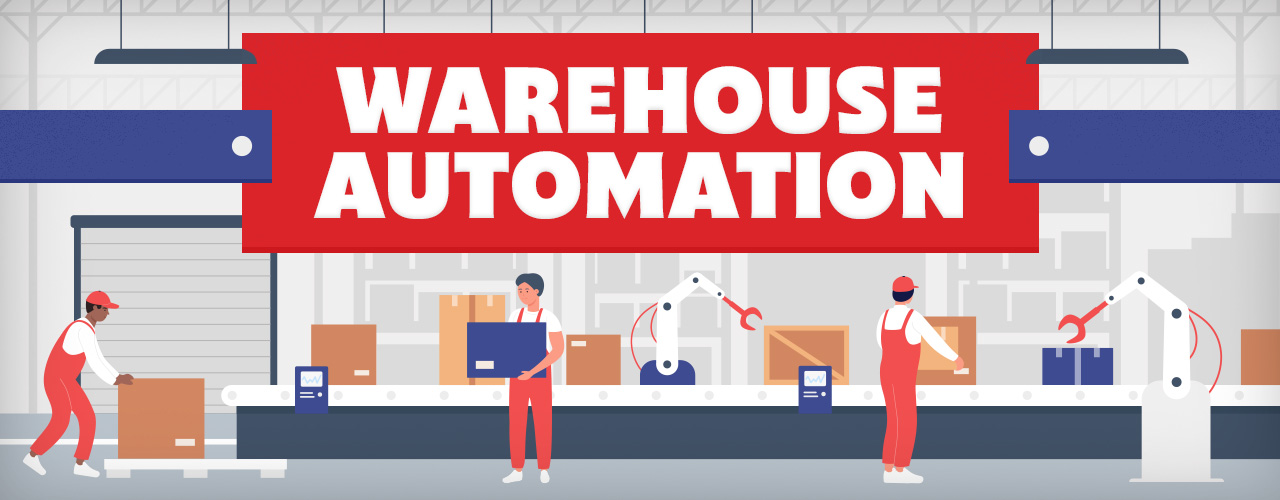
Automation is transforming the warehousing industry. The responsibilities of workers have evolved, error rates are falling, and workplace layouts have changed to adapt to emerging technologies. Whether you're starting a new warehouse or already managing one, staying educated on the topic of automation is essential. In this article, we’ll investigate what warehouse automation is, the different forms it takes, and current warehouse automation trends.
What Is Warehouse Automation?
Warehouse automation is the process of replacing labor-intensive and time-consuming responsibilities in a warehouse with automated systems. No matter what type of warehouse you manage, automation allows your employees to prioritize essential tasks over repetitive ones.
Warehouse Automation Benefits
Below are some common benefits associated with warehouse automation:
- Reduced costs: Automated technologies can complete many tasks faster than humans. They allow you to streamline your production process and reduce waste, keeping your expenses down.
- Increased safety: Automation allows you to limit hazards and promote warehouse safety.
- Sustainability: Some automation systems are designed for energy efficiency. With them, you can reduce wasteful energy consumption.
- Increased employee efficiency: By automating tedious or repetitive tasks, your staff can allocate their time to areas of the warehouse that need it more.
- Spatial utilization: Automated technologies do not require as much space as human workers, allowing you to optimize your warehouse layout.
Warehouse Automation Systems
In general, there are six different types of warehouse automation. Continue reading to learn about each type, the benefits associated with them, and how much they cost.
1. Pick to Light Systems
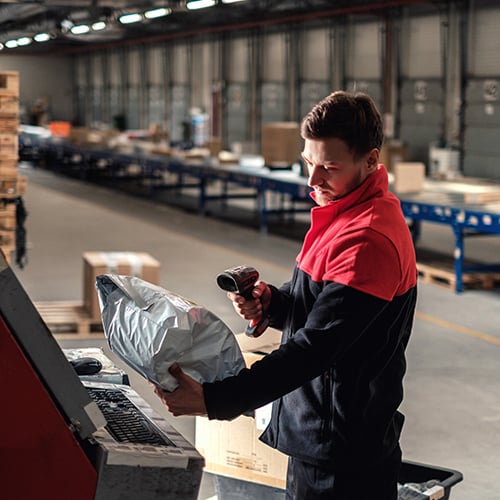
A pick-to-light system, sometimes shortened as PTL system, is a type of automated order-picking technology utilized in modern warehouses. This type of automated technology utilizes LED lights on pallet racks, shelves, and select warehouse surfaces to indicate where order pickers can find a product.
A pick-to-light system starts working when an employee scans a barcode. The system signals an item's location by activating a light in a designated part of the warehouse. The employee then navigates to that location and retrieves the item. It’s important to note that in some cases, the employee must confirm that they received the item by pressing a button or inputting data into a computer.
Pick to Light System Benefits
Pick-to-light systems offer a variety of unique benefits for your workplace. Below, we've listed two of the most prominent:
- Accessibility: Pick-to-light systems are easy to use, facilitating a simple training process.
- Faster picking times: Pick-to-light systems decrease the time employees spend searching for an item.
Pick to Light System Cost
Individual light modules for a pick-to-light system can cost anywhere from $150-250, but the software and equipment needed to make the system work are considerably more expensive. The size of your warehouse can also impact how much you spend. While PTL systems have a high initial cost, they can pay off in the long run.
2. Warehouse Robotics
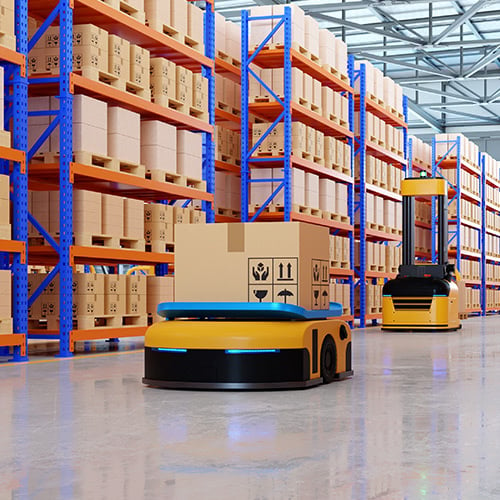
The term warehouse robots is a blanket term for any machine that works collaboratively with human employees. These single-purpose machines support human labor by assisting with particular tasks throughout the warehouse. We’ve listed some common examples of warehouse robots below:
- Automated guided vehicles: Also known as AGVs, these machines transport materials with minimal human oversight. They navigate warehouse floors and reach their destination by following guided paths made from wires, magnetic strips, or sensors embedded in the floor.
- Automated storage and retrieval systems: Often shortened as AS/RS, automated storage and retrieval systems have simplified inventory management. They typically look like cranes or shuttles and run on a fixed track.
- Collaborative robots: Commonly known as cobots, collaborative robots work hand-in-hand with your staff to accomplish goals. Some collaborative robots take the form of a mobile storage bin, while others give workers directions to goods.
- Articulated robot arms: These machines are automated arms that are used to move, turn, and maneuver items throughout the workplace. They can be used in packing stations, as a tool in storage areas, and even aid in pallet racking.
Automated Guided Vehicle Cost
The cost of an automated guided vehicle can range from $15,000 to $80,000. You'll also have to invest in batteries, job control software, and sensors to help the vehicles function correctly.
Automated Storage and Retrieval System Cost
Automated storage and retrieval systems can cost anywhere between $70,000 to $1,500,000. This price is determined by the type of AS/RS you choose. For example, a mini-load AS/RS typically starts at $750,000 while a unit-load AS/RS starts at $1,000,000.
Collaborative Robot Cost
The price of a collaborative robot ranges from $10,000 to $50,000. Cobots can also be fitted with accessories such as sanders, grippers, and measuring sensors, each of which can impact the final price of the unit.
Articulated Robotic Arm Cost
The cost of an articulated robotic arm can range from $25,000 to $400,000. You may have to invest in sensors, controllers, or power sources to help your arm work, which can increase the total price of the unit.
Benefits of Warehouse Robotics
While warehouse robots come in many forms, they share several benefits. We've listed two of the most important benefits below:
- Improved order fulfillment: Warehouse robots allow your staff to fulfill orders with speed and accuracy.
- Improved inventory management: By using robots in your warehouse, you’ll be able to manage inventory with ease and keep your stock counts up to date.
3. Warehouse Drones
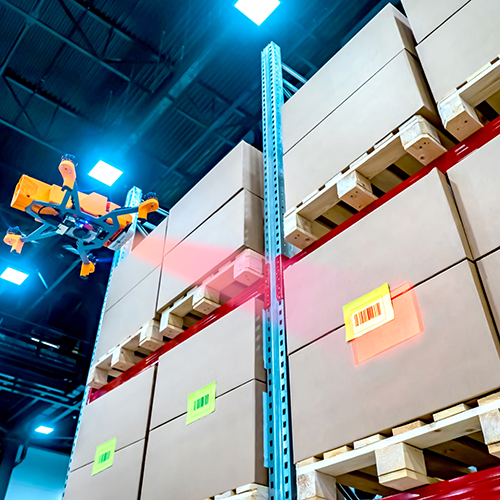
Warehouse drones make inventory management efficient. They can perform inventory audits, count cycles, and even find stock from the air. These drones function autonomously, flying above your warehouse and capturing images that human employees can't. Most warehouse drones come in the form of a quadcopter, a type of unmanned helicopter that features four rotors.
Warehouse Drone Cost
A typical quadcopter warehouse drone can cost up to $1,000. This price can vary depending on the size of your warehouse and the frequency you plan on using the drone.
Benefits of Using Drones in Warehouses
Continue reading to learn how drones can benefit your warehouse:
- Hazard management: Workers will no longer have to climb ladders or work at dangerous heights during inspections.
- Fewer restrictions: Drones can move with more freedom than humans and reach areas that aren’t accessible to your staff.
4. Voice Picking Systems
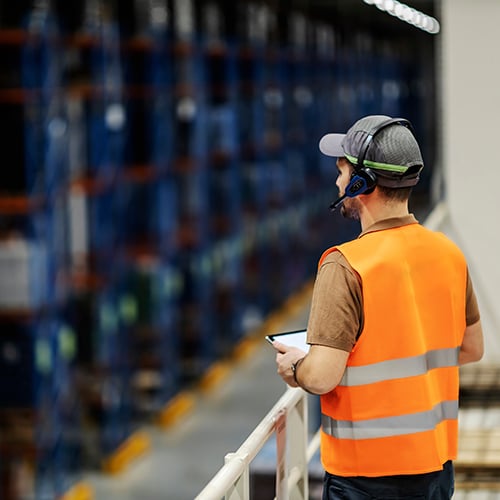
A voice picking system utilizes speech recognition software to make the order-picking process more efficient. These hands-free systems provide employees with voice prompts, directing them throughout your warehouse and giving instructions on what to do. This feedback is typically received through a headset. Employees can communicate with the system by repeating reference codes into the headset to verify the information.
Voice Picking System Benefits
Below, we'll investigate how voice picking systems can improve your warehouse:
- Reduced training times: Employees will learn the layout of your facility as the voice picking system guides them through it.
- Convenience: Voice picking systems are relatively simple to use, and their hands-free design decreases the burden on employees.
Voice Picking System Cost
In general, a voice picking system can cost between $4,000 and $5,000. It’s important to note that along with voice picking equipment, you’ll have to purchase software to help it run.
5. Goods to Person Automation
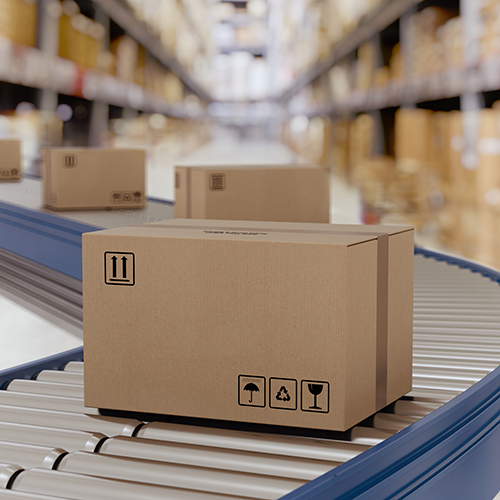
Goods-to-person systems, sometimes referred to as GTP systems, represent a modern order fulfillment strategy. GTP systems combine automatic storage and retrieval methods with an efficient picking process to transport goods directly to your employees. These systems often work in conjunction with a variety of other automated technologies.
Goods-to-person technologies utilize stacker cranes, shuttle systems, and roller conveyors to achieve the best results. The GTP system operator sits at a pick station, where they can pick the units indicated by their warehouse control system.
Goods to Person System Benefits
Below, we've listed some common ways that goods-to-person technologies can change your workplace for the better:
- Decreased possibility of accidents: Employees will be stationed at the same place throughout the GTP process, significantly reducing the risk of a workplace accident.
- Less human error: With an automated system, the chances that an employee selects the wrong item are reduced.
Goods to Person Cost
A goods-to-person automation system can cost between $500,000 and $1,000,000. If the system is utilized correctly, it will provide a return on investment relatively quickly.
6. Sortation Systems
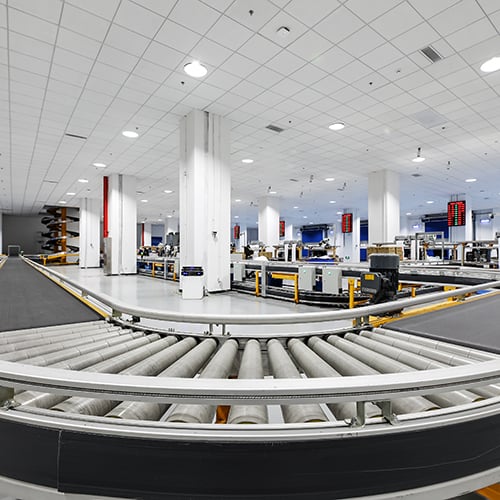
Automated sortation systems identify individual items in your warehouse and transport them to the correct location. They typically utilize a conveyor system and are an excellent way to improve the flow of products through your workplace. In general, there are two different types of automated sortation systems:
- Case sorters: These systems handle completed orders and boxed goods. Case sorters come in many forms including pusher sorters, paddle sorters, and crossbelt sorters.
- Unit sorters: A unit sorter transports individual units rather than entire packages. The most common type of unit sorter is a loop sorter, where items rotate on a closed circular loop.
Sortation System Benefits
We've listed some of the key benefits of using a sortation system below:
- Accuracy: Sortation systems ensure that each product arrives at its desired location.
- Quick transportation: Automated sortation systems facilitate the quick transportation of goods from one part of your warehouse to another.
Sortation System Cost
A typical warehouse sortation system costs between $5 million and $10 million. Costs can vary depending on the number of products you plan on sorting and how large you want the system to be.
Warehouse Automation Trends
As warehouse automation has grown in popularity, several trends have emerged. These trends represent a combination of innovation, convenience, and personal preferences. In this section, we’ll introduce common warehouse automation trends and how they relate to your workplace.
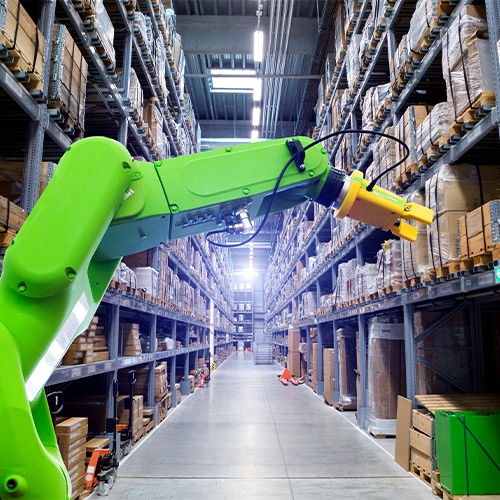
Autonomy
Warehouse managers have shown an interest in using autonomous robots to complete simple, tedious, or repetitive tasks. Autonomous machines take many forms in the warehouse, such as AGVs, autonomous mobile robots (AMRs), and various other devices.
The shift towards autonomous machines rather than traditional warehouse machines represents the need to focus on high-priority tasks rather than repetitive, time-consuming tasks. By utilizing these types of automation, warehouse managers can transform their workplace and improve productivity.
Wearable Technology
Sometimes called wearables, wearable technology is quickly gaining popularity. By integrating warehouse devices in a wearable format, your employees will complete tasks with increased efficiency. Many of these devices can connect to the internet, providing up-to-the-minute data to analyze.
Examples of wearables include the following devices:
- Smart glasses
- Hand-mounted barcode scanners
- Finger-trigger gloves
- GPS tracking bracelets
Industrial Internet of Things
The industrial internet of things, often shortened as IIoT, isn’t a single type of technology. Rather, it is a system that connects all of the automated devices in your warehouse. Beyond that, the industrial internet of things is enabled by cybersecurity, cloud computing, cognitive computing, and a variety of other innovations. This interconnectivity allows data to be collected, analyzed, and exchanged without interruption.
Warehouse Automation FAQ
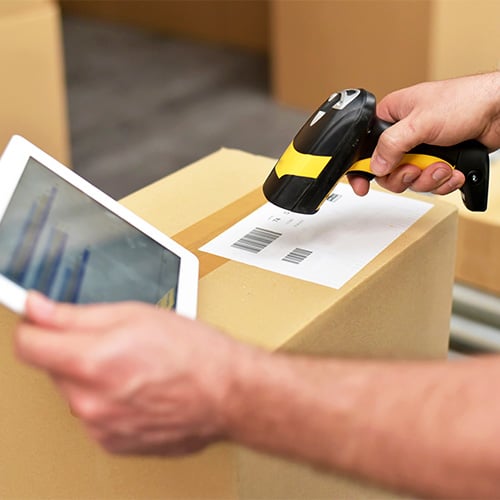
Warehouse automation can be a complicated subject, and there are many questions to be answered about it. We’ll answer some of the most popular questions below:
How Does Warehouse Automation Reduce Costs?
Warehouse automation reduces costs by eliminating select responsibilities in the workplace and ensuring accuracy. As a result, workers can focus on different tasks, waste is reduced, and your warehouse can operate efficiently.
How Are Warehouse Jobs Changing with Automation?
Warehouse jobs have become easier since the introduction of automation. Workers have more time to focus on specialized tasks and generally work in safer environments than they did before. Beyond that, many warehouse workers report that the quality of their jobs has improved.
Back to TopJust as restaurant automation has changed the foodservice industry, the introduction of automated technologies is revolutionizing the warehousing industry. Costs have been cut, tasks are completed faster, and the priorities of workers have shifted. By introducing the technologies above, you can position your warehouse for success.