
A hazard assessment is a crucial process that identifies potential hazards in your workplace procedures and processes before they lead to accidents or injuries. This proactive approach is essential for maintaining a safe working environment and complying with Occupational Safety and Health Administration (OSHA) guidelines. The primary focus of a hazard assessment is on your employees, the tasks they perform, the tools and equipment they use, and their overall work environment. By examining these factors, you can pinpoint potential sources of danger and take appropriate measures to mitigate risks.
Who Is Responsible for Conducting a Hazard Assessment?
Employers are primarily responsible for conducting a hazard assessment in the workplace, as outlined by OSHA guidelines. Depending on the organizational structure of a business, this duty typically falls on the business owner or a senior member of the management team. Once the hazard assessment is complete, the responsible party must promptly address the identified hazards.
What Is a Workplace Hazard?
A workplace hazard is anything within a work environment that has the potential to cause harm to staff or guests. These hazards are typically associated with factors or actions that, if left unchecked, can result in injury or illness. Identifying and addressing workplace hazards is essential for maintaining a safe and healthy work environment.
How to Perform a Hazard Assessment
There are several steps to conducting a thorough hazard assessment. It is essential to remember that each business is unique, and your hazard assessment plan should be adapted to suit the specific needs and operations of your establishment for the best results. To effectively perform a hazard assessment, follow these tips:
1. Collect Workplace Information
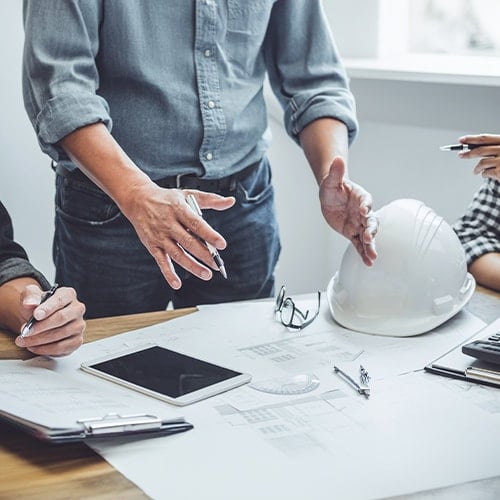
Begin by accumulating as much information as you can about your workplace. Focus on the types of equipment used in your operations, the prevailing conditions of your workplace, and the existing safety protocols in place. This data is a crucial reference point for assessing risks and determining the appropriate actions to mitigate potential hazards. Some of this information may already be available from employees, business records, and other internal resources. If details are not readily accessible, check the following resources:
- Operating manuals: Reviewing equipment manuals provides valuable insights into the proper use, maintenance, and safety precautions associated with specific machinery or tools.
- SDS sheets: SDS sheets, or safety data sheets, contain crucial information about the composition, hazards, and safe handling procedures for chemical substances used in the workplace.
- Self-inspection reports: Previous self-inspection reports can offer valuable data on identified hazards, corrective actions taken, and areas requiring further attention.
- OSHA 300 and 301 logs: These logs document workplace injuries and illnesses, providing insights into past incidents and trends.
- Exposure monitoring results: Data from exposure monitoring assessments helps evaluate employee exposure to hazardous substances or conditions.
- Existing health and safety protocols: Reviewing current health and safety procedures enables you to assess their effectiveness and identify areas for improvement.
- Employee surveys: Gathering employee feedback about safety concerns and observations can help uncover potential hazards that may have been overlooked.
2. Identify Physical Safety Hazards
This inspection allows you to accurately assess the current state of your workplace and pinpoint physical risks. Regular inspections are essential as workplace conditions can deteriorate or change over time. During your assessment, inspect all operations, equipment, work areas, and facilities. Be on the lookout for various physical safety hazards, including:
- Slip, trip, and fall hazards: Uneven surfaces, exposed cables, wet floors, and cluttered walkways pose serious risks.
- Electrical hazards: Damaged cords, overloaded outlets, and faulty wiring can lead to electric shocks and kitchen fires.
- Equipment hazards: Malfunctioning machinery, lack of guarding, and improper use of tools can result in injuries.
- Fire protection: Insufficient fire extinguishers, blocked fire exits, and flammable materials jeopardize workplace safety.
- Workflow issues: Poorly designed work processes, lack of signage, and inadequate lighting will impede productivity and create safety hazards.
- Workplace violence: Hostile behaviors, harassment, and lack of security measures threaten employee well-being.
- Ineffective emergency procedures: Lack of emergency drills, unclear evacuation routes, and outdated response protocols compromise employee safety.
3. Identify Health Hazards
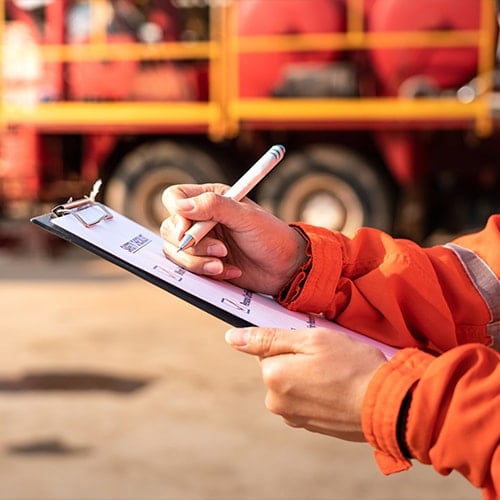
Health hazards differ from physical safety hazards in that they may not always be immediately obvious and can sometimes be more challenging to identify. Some health hazards may not be apparent to the eye and could require specific testing to be discovered. They encompass a variety of risks that can impact the well-being of your employees and can be classified under four categories: chemical hazards, physical hazards, biological hazards, and ergonomic risk factors.
- Chemical hazards: Chemical hazards are substances that cause harm to individuals through exposure. These hazards can often be identified by reviewing Safety Data Sheets (SDS) labels on products used in your establishment.
- Physical hazards: Physical hazards pertain to environmental conditions that pose a threat to the health and safety of your staff. These hazards can be identified by evaluating noise levels, heat levels, and radiation levels within your workspace.
- Biological hazards: Biological hazards involve exposure to living organisms or substances produced by these organisms that can cause adverse health effects. This includes exposure to infectious diseases, molds, toxic substances, poisonous plants, biological materials from humans and animals, and anything that could trigger an allergic reaction.
- Ergonomic risk factors: Ergonomic risk factors relate to workplace design and tasks that could lead to chronic pain or other health issues. Heavy lifting, repetitive motions, and tasks involving significant vibrations are ergonomic risk factors that should be identified and addressed.
4. Identify Emergency Hazards
Hazards from emergencies can be challenging to predict, yet they play a crucial role in conducting a comprehensive hazard assessment. The types of emergencies you could encounter will vary depending on your industry, location, and climate. It is imperative to be proactive in identifying and preparing for these potential emergency hazards. Some emergency hazards to plan for include:
- Fires: Develop fire safety measures and conduct regular fire drills to ensure everyone knows how to respond to a fire emergency.
- Explosions: Explosions can result from various factors such as gas leaks, combustible dust, or chemical reactions.
- Chemical releases: Proper handling, storage, and disposal of hazardous chemicals are essential to mitigate the risks of chemical releases.
- Hazardous material spills: Spills of hazardous materials can occur during transportation, storage, or handling. Implementing spill response procedures and having the appropriate spill containment equipment is vital to minimize environmental and health impacts.
- Infrequent maintenance: Neglected maintenance can lead to equipment failure or structural issues that pose safety hazards.
- Structural collapse: Structural collapse can result from aging infrastructure, poor construction, or natural disasters. Regular structural inspections and addressing any structural deficiencies are crucial for ensuring the safety of occupants.
- Disease outbreaks: Implementing infection control measures, promoting good hygiene practices, and having a response plan for disease outbreaks are essential for protecting the health and well-being of employees and visitors.
- Weather emergencies: Hurricanes, tornadoes, and other natural disasters can disrupt operations and pose safety risks, and you should have a robust emergency response plan in place.
- Medical emergencies: Providing first aid training to employees, maintaining first aid supplies, and having emergency response protocols in place can save lives.
- Workplace violence: Workplace violence can manifest in various forms, including physical assault, threats, or harassment. Implement workplace violence prevention policies, conduct security assessments, and provide training on de-escalation techniques.
- Crime: Criminal activities like theft, vandalism, or armed robbery pose security risks. Implement access control systems, surveillance cameras, and security patrols to deter criminal activities.
5. Investigate Workplace Incidents

When any workplace incidents are reported, whether they involve injuries, illnesses, close calls, or other concerns indicating hazards, they should be thoroughly investigated. Developing a structured investigation plan is essential for obtaining the best results. Both management representatives and employees should be included in the investigative team to provide a comprehensive perspective, and a clear line of communication should be established within the team.
Ensure that the investigative team has the necessary materials and equipment to conduct a thorough examination of the incident. This may include safety gear, documentation forms, cameras, measurement tools, and other resources required to gather data and evidence. Encourage your team to approach the investigation without bias and to focus on facts and evidence. Strive to identify the root cause of the issue under investigation and explore how it could have been prevented.
6. Characterize Hazards and Identify Control Measures
For each type of hazard identified, it is essential to develop control measures that will keep them in check and ensure the safety of workers and guests. Evaluate each hazard, consider the severity of outcomes, and consider the likelihood of an event or exposure occurring. Develop internal protocols that outline clear procedures for responding to different hazards. These protocols should include short-term actions that can be taken immediately and long-term plans for preventing similar incidents. Address hazards that pose the greatest risk first and then work your way down the list until control measures are in place for all identified hazards. By doing so, you can effectively allocate resources and focus efforts on areas that require immediate attention.
Back to TopPerforming a hazard analysis allows you to eliminate or minimize potential hazards, thereby reducing the risk of workplace accidents and injuries. By conducting regular hazard assessments and implementing appropriate control measures, you can create a safer and healthier environment for employees and customers.