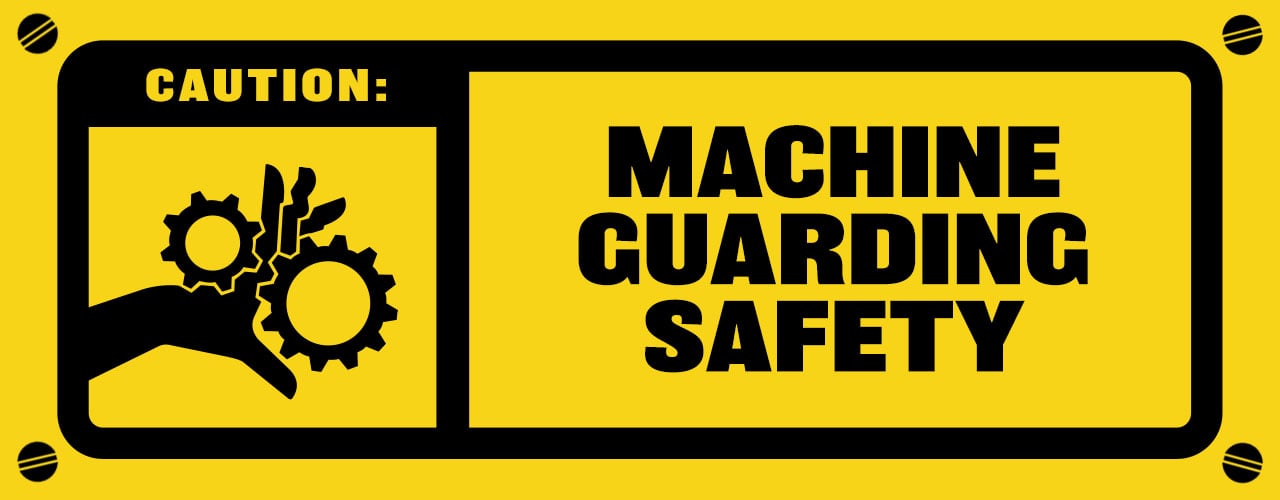
What is machine guarding? Machine guarding is a practice that protects operators and employees from the mechanical hazards of heavy machinery. Whether you're opening a warehouse or managing the safety of a manufacturing facility, you need to be familiar with machine guarding methods. If not properly safeguarded, industrial machinery and parts have the potential to cause serious harm. OSHA states that unguarded machinery contributes to 18,000 injuries and 800 deaths per year. Keep reading to learn about the importance of machine guarding and how you can implement this practice in your workplace.
What Is a Machine Guard?

A machine guard is a safety feature designed to create a physical barrier around moving machine parts that have the potential to cause workplace injuries. Industrial machinery that presents a mechanical hazard is required to have machine guards in place. These guards protect anyone in the vicinity from flying sparks, crushed fingers, lacerations, and amputations. Understanding the basics of machine guards and other safeguard methods will help you establish a successful warehouse safety program.
Types of Mechanical Hazards
Any type of machinery that presents a mechanical hazard needs a machine guard in place. According to OSHA, there are three types of mechanical hazards.
- Hazardous Motions - Hazardous motions are moving parts of machinery that rotate, slide, or move in a continuous line.
- Points of Operation - The point of operation is the location on the machinery where the material is cut, shaped, stamped, or bored.
- Pinch Points and Shear Points - Pinch and shear points are areas where limbs, digits, hair, or clothing can get caught between two parts.
What Is a Nip Point?
A nip point occurs when two machinery components move towards each other and create the possibility for any foreign object to get caught between the parts. Common nip points are caused by rotating gears, rollers, and pulleys. Hair, loose clothing, and body parts can become caught and drawn between the two components. Nip points are one of the leading causes of serious workplace injury when dealing with heavy machinery because they are not always obvious at first glance. Amputations, lacerations, and even death can occur when these locations are left unprotected by a machine guard.
Nip Point vs Pinch Point
The terms nip point and pinch point are often used interchangeably but there is a slight difference between the two. A pinch point is any location where a foreign object can be caught between two parts. A nip point is a specific type of pinch point that occurs with rotating parts like gears and pulleys.
What Are Non-Mechanical Hazards?
Some hazards are caused by non-mechanical sources. This means that the danger isn’t coming from a moving part or motion but from fabricated stock and waste materials. Non-mechanical hazards include flying sparks, chipped metal or wood, and splashes from hot or molten material. Warehouse PPE should be used in these environments, and machine guards should be installed anywhere these types of hazards are present.
Types of Machine Guards
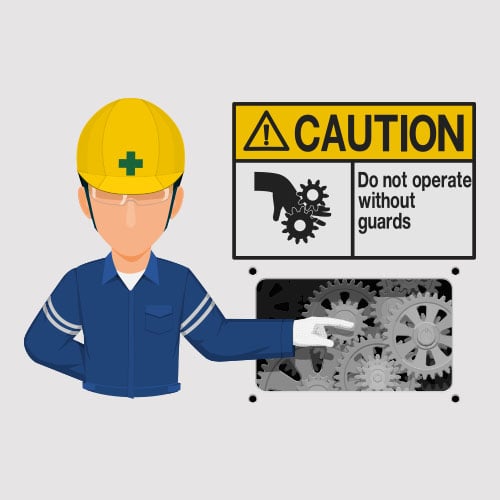
Employers are responsible for making sure machine guards are in place. These guards can be fabricated in-house or purchased from suppliers. Each piece of machinery has its own requirements based on the types of mechanical and non-mechanical hazards that are present. These are the four most common types of machine guards in the industry:
1. Fixed Guards
A fixed machine guard is a permanent part of the machinery and doesn’t interfere with operation. Many fixed guards follow the contours of the machinery and come in the form of a fence or blade cover. This type of machine guard provides the most protection and requires little maintenance, but may interfere with visibility during operation. A fixed machine guard should display the following criteria:
- Must fully enclose the hazardous part of the machine
- Must be firmly attached and cannot be removed without disassembly
- Should not present a new hazard to the operator
- Must be made with strong, durable materials that can withstand impact and vibration
- If needed, should allow for airflow and ventilation
2. Adjustable Guards
Adjustable machine guards can be modified by the user. This type of machine guard is common with cutting tools that manipulate raw materials. Items are fed into the machine and clearance needs to be adjusted to accept materials of different sizes. For certain types of machinery, like cutting saws and drills, this is the only type of machine guard that will work. Adjustable guards provide flexibility, but operators should go through extensive training before using them.
- Employees must be trained to operate this type of guard safely
- Guard is adjustable to accept different types of materials
- Dangerous points of action for cutting or drilling are not completely protected
- Other safety measures should be in place to help protect the user
3. Self-Adjusting Guards
A self-adjusting machine guard changes position to allow the fabrication of materials, then moves back into a default position when the material is removed. This is a safer option than an adjustable guard because the guard adjusts automatically without any help from the user. Less training is required to operate machinery with self-adjusting guards, but access to dangerous machine parts is still possible.
- Guards adjust automatically
- Requires less training for safe operation but may need more maintenance
- Dangerous points of action for cutting or drilling are not completely protected
- Other safety measures should be in place to help protect the user
4. Interlocking Guards
Interlocking guards are designed so that when the guard is disengaged or removed, the power to the machinery automatically shuts off. This prevents anyone from placing their hands near dangerous moving parts when the machine is operating. OSHA recommends that any removable guards that are not fixed in place should be interlocked with the machinery to prevent injury.
- If the guard is open, power to the machine is cut off
- The machine must be restarted with the guard in place
- Prevents workers from placing hands near hazardous motions or points of action
- Provides the same level of protection as a fixed guard with more flexibility
Safeguarding Methods
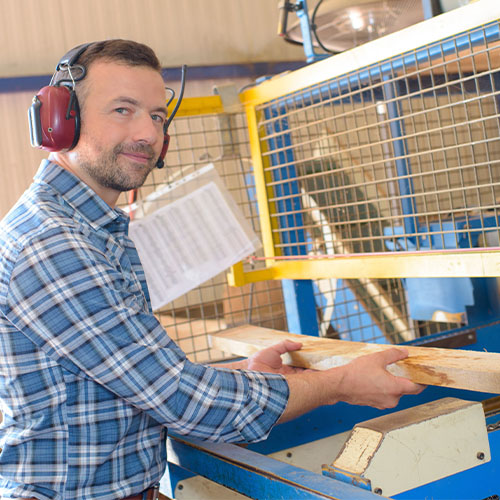
Machine guards are just one method of safeguarding heavy machinery. The practice of machine guarding also includes these other methods and devices:
Devices
Devices are safety items that are used to protect operators while they use machinery.
- Pullback Devices - A pullback device attaches cables to a user's hands and allows access to the point of operation when it's safe, but pulls the arms back when the point of operation becomes unsafe.
- Restraint Devices - A restraint device attaches to the user's hands and keeps them at a fixed point to avoid a dangerous motion.
- Gates - A gate device is a movable barrier that is interlocked with a machine to prevent contact while the machine completes a cycle or downstroke.
- Safety Controls - Safety controls require that the operator keeps each hand on a control button while the machine completes a cycle. If the control buttons are released, the machine will deactivate.
Automated Feeding and Ejection Mechanisms
Automated systems designed for feeding materials can be used in place of manual operation to remove the danger to employees. Replacing human labor with robotics and automation eliminates risk, epsecially for tasks that involve heavy machinery.
Machine Location or Distance
Safeguarding can be performed simply by using distance as the safety measure. Machinery and dangerous points of motion aren't accessible if they are located out of reach.
Many factors play into the safety needs of each industrial environment, from the types of machinery present to how you set up your warehouse. A good safety program should cover trainings on safety signs, safety acronyms, and machine guarding. This ensures you stay OSHA-compliant and protect your workforce.