Drum Handling Equipment
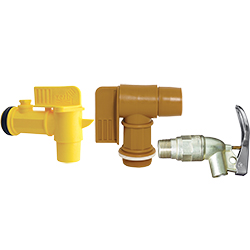
Drum Accessories
Shop Drum Accessories
44 Products
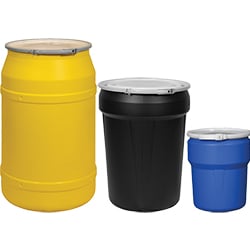
Industrial Drums
Shop Industrial Drums
87 Products
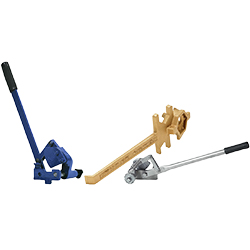
Drum Openers
Shop Drum Openers
14 Products
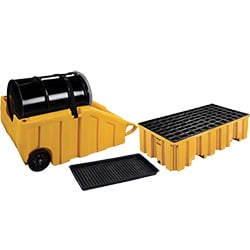
Spill Containment
Shop Spill Containment
67 Products
Top Products
Other Material Handling Equipment
If you work with 30, 55, and 85 gallon steel drums, we have essential drum handling equipment to assist in your day-to-day tasks. Choose from an array of sturdy steel drum trucks and dollies to easily maneuver steel drums around your work space. We offer drum deheader equipment so you can open your steel drums with minimal effort. You can also find a variety of steel drum faucets and wrenches to help you improve the efficiency of your warehouse. Keep your employees safe by adding hard hats, warehouse gloves, and emergency lights and exit signs to your facility.
Transport Heavy Drums With Ease by Using Drum Handling Equipment
Make moving heavy loads simple with the help of our drum handling equipment. Whether you’re transporting, filling, or emptying drums in your establishment we have drum handling equipment to help you get the job done. By implementing this equipment in your facility, you can reduce the strain and effort exerted by your employees and make your establishment an overall safer work environment.
Additional Resources