Silica gel is a mixture of water and silica (a common mineral found in sand, quartz, granite, and other minerals) that forms into tiny pellets when combined. Silica gel is a type of desiccant that holds water vapor at its surface instead of fully absorbing it. Each silica bead has thousands of tiny pores that retain moisture, making silica gel packets perfect for placing in boxes with products to control humidity.
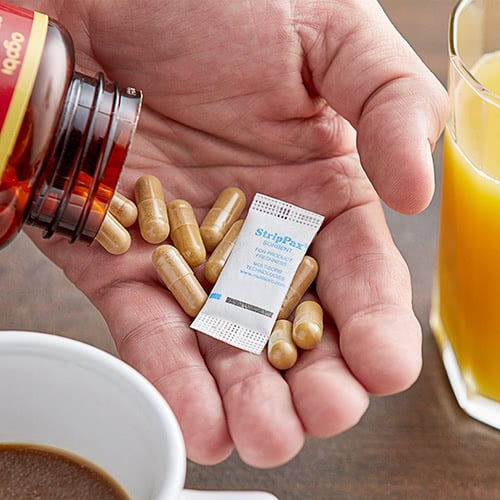
What Is Silica Gel Used For?
Silica gel is used for controlling humidity, making it a great addition to product boxes that are being shipped to customers. Some examples that should have silica gel packets included in their box prior to shipping are the following:
- Electronics
- Clothing
- Leather
- Vitamins
- Cat litter
- Paper
- Food and baked goods
People also use silica gel packets to dry flowers or prevent rust from forming on tools!
Where to Buy Silica Gel
Silica gel packets can be purchased at home improvement stores or from specialty online retailers.
Shop All Silica Gel Packets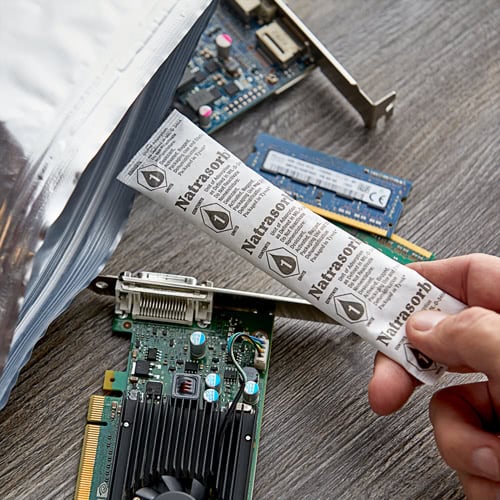
How Does Silica Gel Work?
Silica gel’s natural adsorbing properties hold water molecules to its surface. Silica is covered in millions of tiny pores that retain about 40% of its weight in moisture, reducing the humidity in a closed container.
Is Silica Gel Poisonous?
Silica gel is not safe to eat. If silica gel is placed in the mouth, spit beads out immediately. If swallowed, it’s best to go to an emergency room just in case. Not all silica gels are created equal, and some have a toxic coating called “cobalt chloride”. This chemical can cause abdominal pain and vomiting.
Silica gel packets are a choking hazard for small children, so store unused packets in a secure area.
How Much Silica Gel to Use
When considering how many silica gel packets to put in your container, a good estimation to use is 1.2 units of silica gel packets for every 1 cubic foot of volume in the space of your box. There are other considerations to take into account as well, such as the materials being shipped, how long the products need to be protected, and the climate of where your product is being shipped.

Is Silica Gel Safe for Food Storage?
Yes, food-grade silica gel packets are safe for food storage. Silica gel removes excess moisture, making it great for use in your spice drawer and in packets of seaweed, dried fruit, or jerky. It's also great for potato, garlic, and onion storage drawers to slow down sprouting.
Silica gel packets are extremely beneficial for shipping products like food, tools, clothing, and so many other materials. Next time you are worried about maintaining the integrity of your product from your warehouse to a customer’s front door, consider using high-quality shipping materials and adding silica gel packets to your boxes!
Related Resources
Warehouse Safety
If you are opening a warehouse, getting every single detail right can seem daunting, and knowing what to prioritize is even more challenging. When it comes to the safety of your employees, we’ll make it simple for you: before employing your warehouse staff, you need to strategize and implement warehouse safety procedures around your facility. Once you've hired your employees, educate them on popular safety acronyms so they can evaluate risks and respond to emergencies. Below we have outlined the various warehouse safety standards set by the Occupational Safety and Health Administration (OSHA) so you can be certain that your warehouse safety is good to go. Select which section interests you: Commonly Cited Hazards Warehouse Safety Topics Additional OSHA Safety Topics OSHA’s 10 Most Commonly Cited Warehouse Safety Hazards If OSHA finds a safety violation in your warehouse where safety standards are not being met, they will issue a costly citation. Below is a list of OSHA’s most common warehouse citations: Forklifts Hazard communication Electrical, wiring methods Electrical, system design Guarding floor & wall openings and holes Exits Mechanical power transmission Respiratory protection Lockout/tagout Portable fire extinguishers Back to Top Warehouse Safety Topics To reduce the probability of being cited for one of OSHA’s most common citations, follow OSHA’s guidelines list below (found in their Warehousing Safety Brochure) on reducing hazards in specific areas of the warehouse: 1. Forklift Safety Understanding and training your employees on proper forklift safety is extremely important. According to OSHA, about 100 employees are killed and 95,000 are injured every year while operating forklifts. In fact, it is best to avoid working at heights unless absolutely necessary, especially when considering forklift and even ladder safety. Apply the same rules as driving a car to driving a forklift such as paying attention to speed limits, wearing a seatbelt, and watching where you are driving. If anything, more caution should be taken while operating a forklift as workers walk freely throughout the warehouse. Below are a few solutions to avoiding forklift hazards according to OSHA: Ensure that all employees can operate forklifts safely by providing proper training, evaluation, and certifications for all operators Create safe clearances for forklifts in aisles and loading docks, and prevent noxious gases from forming by ventilating parked forklift areas Maintain the quality and upkeep of a forklift by checking for hazards before driving and examining hazardous conditions 2. Loading Dock Safety An elevated surface can create more hazards than one might think. Products falling on employees, improper use of equipment, and being unaware of the dock’s edge are just a few problems that can happen in the loading dock area. With that, it's important that traffic control plans are developed to avoid collisions. Loading dock edges should be properly lit and marked with visual warnings as helpful visuals for drivers and employees. Guard rails should also be installed for further protection for employees, to discourage jumping, and other poor ergonomics or horseplay. Another consideration is proper ventilation to prevent noxious fumes from forming. Below are OSHA’s recommendations on avoiding potential loading dock hazards: Make sure to secure the dock plates and check to see if they can safely support the load Dock edges should be clear and have signs that provide visual warnings 3. Conveyor Safety Because conveyor belts are ongoing machines, they pose a wide variety of potential hazards to your employees. Risks like clothing or jewelry getting caught, standing and falling off the conveyors, and items getting stuck in the belt can pose very unsafe threats for your employees. Make sure employees are wearing mandated safety uniforms to reduce the risk of clothing getting caught, while training them on the dangers of standing, sitting, and walking on the moving belt. It's also important to note that if items are caught in the belt, a lockout system is initiated instead of trying to resolve the problem while the conveyor belt is still operating. From being caught in pinch points to products falling off the belt, find out how to deflect common hazards with conveyor safety solutions as outlined by OSHA: Identify pinch points and ensure they are adequately guarded Create systems that lockout conveyors and train employees in these procedures 4. Material Storage Safety Properly stacking and storing materials using material handling equipment is imperative when working with tall shelving units in your warehouse. Keep in mind proper box and pallet stacking patterns to maximize space and secure storage. When stored improperly, the materials may fall and injure workers. Properly storing equipment, such as ladders, also prevents workplace accidents and prolongs the life of the equipment. Because of this, you'll want to supply your workers with PPE such as thick gloves to avoid sharp edges and steel-toed safety boots to prevent foot injuries. Other great products to supply your employees with are handles or holders that can be attached to heavier loads as it makes it easier to maneuver the load and reduce any pinched fingers. To avoid these maladies, follow OSHA’s safety guidelines for material storage: Boxes need to be stacked straight and evenly, and the heavier loads should be stacked on the lower or middle shelves Aisles and passageways need to be clear of any objects 5. Manual Lifting Safety Protecting your employees’ well-being is paramount to being a good employer and keeping your workers employed. During a laborious job, your employees can sustain short- or long-term injuries from improper lifting or overexertion. Luckily, there are a lot of ways to eliminate this! Before onboarding employees, focus on the design and function of the work environment to fit employees' physical requirements, such as safety devices, lighting, tools, and other aspects of the various workstations. Checking these ergonomics and structuring them with employees in mind reduces repetitive motion injuries and other stressors. In short, you need to make the job as easy as possible for them to carry out. OSHA’s solutions on avoiding improper manual lifting and handling should be instilled into your daily operations: Mandate training for general ergonomics and encourage employees to help/ask for help when a product is too heavy Eliminate or minimize the need for lifting by acquiring well-designed engineering techniques 6. Hazard Communication Standard Hazardous chemicals can be common in certain types of warehouses. The Hazard Communication Standard (HAZCOM) is a requirement by OSHA for employers in the United States to disclose hazardous substances in a workplace. Being cautious of where these are present in your facility and knowing how to take action when spills of hazardous materials occur is extremely important for your employees’ safety. Below are solutions from OSHA for dealing with hazardous materials and how to prevent them in the first place: All chemicals in the warehouse should have Material Safety Data Sheet (MSDS) with instructions on how to handle the chemicals Write out a spill control plan and have spill cleanup kits present anywhere that the chemicals are stored Train each employee about the hazards of the chemicals being stored, how to properly wear their PPE, and how to clean up the spills 7. Battery Charging Station Safety While charging stations are important for energizing your electric equipment, they can also pose dangerous threats if not treated with caution. These stations house powerful fueling operations such as gasoline, batteries, and liquid petroleum gas. Hazards like fires and explosions are possible if guidelines and general safety aren’t followed around these stations. Taking preventative measures to avoid hazards in your charging station are outlined in OSHA’s guidebook as follows: Forbid smoking or any open flames in charging station areas and keep fresh air flowing or adequate ventilation to prevent noxious gases from forming Follow procedures for refueling gas or propane forklifts and provide readily available and fully charged fire extinguishers Install an eyewash station and safety shower for employees to use in case of exposure to battery acids 8. Ergonomics Safety Along with improper manual lifting, employees can also injure themselves from continuously performing repetitive motions or injure themselves from poor design of the operation. While there is training that can be done to show your employees how to perform their tasks safely, there are also machines and tools to look into for additional security. Some machines to check out are tilters, tilted pick trays, and back saver lifts. All of these heavily reduce repetitive motions like bending and twisting. Tilters position boxes so the contents are easier to access instead of bending in, reaching, and pulling contents out over and over again. Tilted pick trays help workers see the items that are higher up on the pallet track so they can pick the boxes with confidence instead of scaling beams or reaching into boxes blindly and wasting time. Finally, back saver lifts are perfect for your employees who lift, stack, and assemble all day long. These machines help with positioning and pallet picking! To keep your employees safe and healthy both short and long term, follow OSHA’s solutions for proper ergonomics in the warehouse: Eliminate lifts from floor to shoulder height by raising the shelf or bin Educate employees to lift with their legs and keep their backs in natural positions Encourage employees to test the load before manually lifting to ensure they can handle the weight and size and decide which lifting method they should use Back to Top Additional OSHA Safety Topics To further strengthen your warehouse safety standards, we have outlined additional advice and solutions that you can implement in your facility: 1. Provide Appropriate PPE According to OSHA’s PPE Brochure, employers are responsible for evaluating their warehouses and assessing what PPE is needed to keep employees safe. Here are the steps to follow to decide what PPE is necessary for your business: Performing a “hazard assessment” of the facility. To first decide what safety measures need to be taken, it's important to identify the hazards around your facility. A hazard assessment is just that. A hazard assessment identifies both physical hazards (such as moving objects, intense lighting, electrical connections, etc.) and health hazards (such as excessive dust and exposure to harmful chemicals or radiation). Identifying and providing appropriate PPE for employees. After the hazard assessment, analyze the data to determine the proper PPE needed at the warehouse. Familiarize yourself with the different types of PPE available as well as the different levels of protection. You can never go wrong with selecting PPE that will provide more protection than the minimum required so you can keep your employees safe from hazards! Training employees in the use and care of the PPE. Demonstrate to each employee how to properly wear and use PPE before they work. If you notice that an employee who has received training is not practicing the proper use of PPE, that employee needs to be trained again. You should also retrain employees if the warehouse changes or new PPE needs to be used to complete tasks. Maintaining PPE, including replacing worn or damaged PPE. According to OSHA's PPE Handout, employers must provide and pay for PPE as well as replace PPE as needed to keep workers safe. Encourage your employees to talk to management immediately when PPE is damaged, and keep a supply of extra PPE on hand to quickly remedy these situations. Periodically reviewing, updating, and evaluating the effectiveness of the PPE program. Schedule regular, periodic times to reassess your facility for changes in equipment use, operating procedures, and other conditions that may affect occupational hazards. It’s also recommended that you review injury or illness records to find patterns that could be addressed, as well as evaluate PPE to assess its current condition. 2. Mandatory Signage OSHA’s signage guidelines inform employers of the types of warehouse signage that are needed, where they should be placed around the facility, and how to properly display them. There are many different categories that your safety signs will be needed for: notice, general safety, admittance, fire safety, and non-hazard. Each sign present should have one of three levels of classification: caution, warning, or danger. Caution Signs: Potentially hazardous area that may cause minor injuries. Warning Signs: Area that requires special attention and may have unexpected hazards. Danger Signs: The most hazardous area that could have life-threatening conditions. 3. Fire Prevention Plan Create a fire prevention plan to eliminate any potential risk for fires in your warehouse. Follow OSHA’s fire prevention plan requirements for a list of what to include in your plan, including fire prevention supplies you may need. This plan should be written out and kept in the workplace, making it readily available for an employee to review at any time. As an employer, you are also required to inform each employee about fire hazards they are exposed to and review the fire prevention plan with them as well. 4. Emergency Action Plan An emergency action plan (EAP) is a written document that outlines the actions that should be taken by employers and employees during a workplace emergency. Develop an EAP according to OSHA’s standards, and train your employees with the EAP plan and update as needed. For a more detailed list of these requirements, check out OSHA’s EAP minimum requirements page. 5. Standard Operating Procedure (SOP) A Standard Operating Procedure (SOP) is a list of step-by-step instructions outlined by an employer to assist workers with routine tasks. SOP’s are essential for businesses as they reduce failures of complying with industry regulations and reduce miscommunication. SOP’s promote efficiency, performance quality, and consistent output results. Back to Top Besides costing potentially thousands to ten thousands worth in damages, turnover, loss of sales, and lawsuits, keeping your employees safe for the simple matter of maintaining their quality of life is the number one factor of why warehouse safety matters. According to OSHA, the fatal injury rate for the warehousing industry is higher than the national average for all industries, so it is imperative to follow the warehouse safety standards set by OSHA.
How to Set Up a Warehouse
If you've outgrown your current space, starting your own warehouse could be the next logical step in storing and selling your company’s products online. Or it could be a profitable new venture to create a warehouse and rent out your space to other businesses. No matter what your business goals are, setting up a warehouse from scratch requires some careful planning. The layout and allocation of your space need to be mapped out early on. We’ve created this warehouse layout guide to help you set up any type of warehouse for maximum efficiency. Shop All Industrial Supplies Click below to learn more about basic warehouse design: Inbound Loading Dock Receiving Storage and Putaway Picking Shipping Outbound Loading Dock Other Warehouse Spaces Common Warehouse Layouts Warehouse Layout Before you being laying out the schematic of your warehouse, you should be familiar with the essential functions of a fulfillment center and the equipment used to handle materials. Goods come in, they get put away in storage, and they get picked for shipping. To make this happen, the goods flow from one section of the warehouse to the next. Your warehouse setup will be the most successful if you provide space for the following locations: 1. Inbound Loading Dock The loading dock, also called a receiving dock or loading bay, is the entry point where inbound trucks deliver goods to your warehouse. On the exterior of the building, a large parking area provides room for trucks to back up to the building. The dock floor is built to be flush with the truck beds so workers inside the building can enter the trailer with forklifts and pallet jacks. Loading Dock Layout Tips The parking area outside the dock should provide enough room for the largest trucks to turn around and back up to the loading bay. Dock height should be based on the bed height of the most common delivery vehicle used. Consider the number of pallets you'll be unloading during peak delivery times and allocate space for the goods and the loading dock equipment. 2. Receiving The receiving process begins as soon as goods are unloaded on the dock. Shipments are inspected, invoices are checked, and permanent storage locations are assigned for each item. By allocating a holding space for these tasks to be performed, you avoid bottlenecks when multiple shipments arrive at once. A successful receiving area should be located right next to the inbound loading dock. You’ll need space for pallets and boxes to be unloaded and a temporary space for receiving tasks to be performed. The receiving manager needs a home base to work from, which might include a permanent desk with outlets for a computer and room for filing cabinets if you use paper invoices. Receiving Area Layout Tips You can make your receiving process more efficient by including space for temporary holding locations where goods can be staged before putaway. Allow space for performing a thorough quality control check before goods are put in storage. Catching any defects or damage now will help you in the long run. 3. Storage and Putaway Most of the square footage in your warehouse will be dedicated to storage space. When you look at your warehouse space in terms of cubic feet, your storage area should take up between 22% to 27% of the total warehouse space. That percentage may sound small, but it’s because cubic feet accounts for all the vertical space in between the floor and ceiling, not just floor space. For maximum efficiency, you’ll need to take advantage of the clear height of your warehouse. What Is Clear Height in a Warehouse? Clear height is the maximum usable vertical space in your warehouse where goods can be stored. The clear height in your building will be lower than the ceiling height and must account for sprinkler systems or ductwork. Storage Area Layout Tips Take advantage of the available clear height by using pallet racks and industrial shelving to store goods vertically. Using warehouse management system software helps you to maximize your storage space and assign locations. Aisles in your storage area need to be wide enough to accommodate pallet jacks (4' to 5' wide) and/or forklifts (12' to 13' wide) Don't forget to install the proper lighting in your storage area so that goods are visible to order pickers. 4. Picking Picking is the process of retrieving goods from storage to fulfill customer orders. The warehouse employees that perform this task are called pickers. Your picking area is the home base for order pickers — it's the place where they receive their list of items and where they bring orders that are fulfilled. Picking should be located very close to the storage area and may even share some square footage. The picking area should have enough room to store picking equipment like forklifts and pallet jacks. You'll also need space for the picking manager's desk and computers for accessing the warehouse management system. Picking Area Layout Tips Add space in your layout for roller conveyors to carry fulfilled orders from picking to shipping. If your warehouse is small and you don't store items on pallets, shopping carts and shopping baskets can be used to collect smaller items during picking. 5. Shipping After orders have been picked, they are sent to the shipping and packaging area to be boxed up for fulfillment. The shipping area should be close to your storage and picking locations so that goods flow efficiently from one area to the next. Make space in your shipping area for shipping stations — work tables that are set up with all the shipping supplies your workers need to package goods. Shipping Area Layout Tips Besides shipping stations and packing tables, you’ll need space to store your backup inventory of shipping boxes and supplies. It can be helpful to add space for order staging, or organizing shipments by carrier so they are ready to be loaded onto outbound trucks. 6. Outbound Loading Dock The outbound loading dock is the end of the line for your products. It's the exit point where goods are loaded onto trucks for shipping. Just like the inbound loading bay, the outbound bay area should be the same height as the truck beds that back up to the dock. Pallets that are staged in the shipping area can be quickly moved onto trucks and then onto their final destination. Creating two loading bays (inbound and outbound) in your warehouse is necessary for a couple of reasons. For efficiency, goods should always be flowing forward in your warehouse. If you use the same dock for shipping and receiving, you will have goods moving both ways, which creates space issues and confusion. You also have to consider the truck yard and how many trucks are coming and going from your warehouse. Separating the inbound and outbound traffic helps alleviate bottlenecks. Outbound Loading Dock Layout Tips Include plans for proper ventilation on your loading dock because idling trucks create a lot of exhaust fumes. Organizing outbound shipments by carrier type helps to make shipping more efficient. Provide enough space for your outbound loading equipment like pallet wrap machines, pallet jacks, and dock ramps. Other Warehouse Spaces There are other warehouse spaces you'll need to include in your building layout. These locations aren't related to the product cycle but are necessary for business operations. Returns No one wants to think about their products being returned, but it's a fact of life that returns will happen, and they need to be processed the right way. A separate space for processing returns helps to keep those items segregated from the other products in your warehouse. Returns require their own receiving, inspection, and putaway process. Offices In smaller warehouses environments where you are the owner and operations manager all-in-one, you might not need a dedicated office space. Sometimes a desk on the floor of the warehouse or a mezzanine will do. But in other cases, where you have a diversified team of managers and supervisors, it's useful to have office spaces for conducting phone calls, meetings, and administrative duties. Breakrooms Your employees need a place to take breaks, eat their lunch, and store their personal belongings. Designing a space for your workers to unwind when they are off the clock is important for job satisfaction and employee retention. Restrooms Restrooms are essential for any business. You'll need to base the number of restrooms in your warehouse on the size of your workforce. If you have under 15 employees, one restroom might be sufficient. OSHA provides guidance on their restroom and sanitation requirements page. Maintenance and Parts Outside of the storage space needed to hold your products, you'll need a space to store all the parts and replacements that keep your warehouse running. Items like lightbulbs, hardware for industrial equipment, and tools for performing maintenance should all have an organized home in your warehouse. Types of Warehouse Layouts If you are building a warehouse from the ground up, there are three popular layouts that you can rely on when you plan your schematic. These designs all feature a universal rule — keep the inbound and outbound docks separated. U-Shaped Warehouse U-shaped warehouses are very common. The layout is similar to a semi-circle, with the inbound loading dock on one side and the outbound dock on the opposite side. Storage and picking are usually stationed in the center. Products are delivered on one side of the U and flow in one direction to the other side. I-Shaped Warehouse In the I-shaped layout, also called a through-flow layout, the warehouse is shaped like a large rectangle. The inbound dock is positioned at one end of the rectangle with the outbound dock on the opposite side. Storage is located in the middle of the rectangle. L-Shaped Warehouse The L-shaped warehouse also positions the inbound and outbound docks on opposite sides. The flow of traffic and goods move from one side of the L to the far side, with storage located in the "corner". With the increase of consumer online ordering and e-commerce fulfillment, warehouse space has become very valuable. If your business is outgrowing a garage or stock room, it might be time to think about building your own warehouse space to store and distribute goods. Keep all the essential warehouse functions in mind when you create a layout and don't forget to account for future growth.
Shipping Tips for Small Businesses
Large companies lure people with fast, free shipping, but the modern, values-driven consumer prefers shopping small. If you can offer the same speed, efficiency, and convenience as bigger brands, you can run a successful e-commerce business. Use our shipping tips for small businesses to outperform online retailers and expand your reach. Shop All Shipping Supplies Navigate to the small business shipping information that interests you: Shipping Tips Best Shipping for Small Businesses Small Business Shipping Companies 3PL Explained Types of Shipping Packaging How to Calculate Shipping Costs Small Business Shipping Tips Use our small business shipping tips to save money, protect your products, and create a social media-worthy unboxing experience. Establish a Business Shipping Account - Many shipping companies offer expense tracking services, online tools, and discounts when you set up a business account with them. Include Padding - Padding protects your products. There are numerous packing material options, including environmentally friendly solutions, so choose one that works best for your business. If Applicable, Add Insulation/Cooler Packs - If you’re shipping baked goods or other perishables, you must line the box with reflective, insulating material and add freezer packs to keep them cool during transit. Freezing the item itself before you add it to the box helps preserve it. Add-Ins - Add-ins encourage repeat sales. Consider including a free sample of a different product, a printed postcard of your brand values, or a recipe to go with your food item. Handwritten Note - A handwritten note thanking the customer for supporting your small business makes them feel good about shopping with you over a larger company. Personalize 4" x 5" cards with your logo on the front and leave the back blank to write messages. Flat-Lay - Your shipping box is the e-commerce equivalent of a window display. Carefully lay out your products, inserts, and packaging materials to tell your brand story. Create a clean background, add pops of color, and highlight the most important features. Purchase a Thermal Label Printer - Thermal label printers save time by allowing you to print off the labels your shipping service provides. Many thermal label printers connect to laptops via an adaptor or Bluetooth. Once printed, place the label with maximum visibility in mind. Brand Your Box - You can either custom order branded shipping boxes, or you can print a branded logo to display on your box. If customers can identify your package as soon as it arrives, it will build their anticipation and excitement. If your product is perishable or temperature sensitive like chocolate, branded boxes prompt customers to open and/or refrigerate goods upon arrival. Use a Shipping Broker - You can secure the best shipping rates by using a shipping broker. A shipping broker secures bulk shipping rates and makes the discounted rates available to their customers. Invest in Insurance and Tracking - Insurance and tracking provide recourse if your product is lost or damaged. UPS and USPS priority offer complimentary coverage up to $100. Remember Customs and Declarations Forms - If you’re shipping products internationally, you must include customs documentation forms. You can find these at the post office or on your carrier’s website. Check with the US postal service to confirm which forms and labels your international shipment requires. Be Selective About Which Shipping Services You Offer - If you’re shipping chocolate or another heat-sensitive item, suggest the best service for the customer's order. You should deny any shipping option that would lead to your customer receiving a ruined product. Best Shipping for Small Business From free shipping to flat rate shipping, there are a lot of shipping options for small businesses. Whichever you choose, providing transparent shipping prices throughout the purchasing process is vital to your success. According to a Statista study, stores lose over 75% of sales from cart abandonment, and the number one reason for cart abandonment is unexpected shipping fees and high shipping costs. We explain the pros and cons of five different shipping options for small businesses so you can decide how to price your shipping service. How to Offer Free Shipping for Your Small Business To prevent customers from abandoning their cart when they see the shipping costs, many businesses choose to offer free shipping. But as your mother may have told you, there is no such thing as free! Either you or your customer will pay for the “free shipping.” This leaves you with three options: you can increase the price of your products to cover the shipping, you can pay the shipping fees out of your margin, or you can split the cost of shipping with your customers by raising your prices to cover half the shipping. Building shipping into your pricing structure and offering “free shipping” on all your products results in some wins and some losses, but it usually evens out. If this isn’t a viable option for you, consider offering free shipping when the customer spends a certain amount. Choose a price above your average order value that will offset your margin of loss. Free shipping as a reward for high-priced orders encourages patrons to try more of your products and provides the profit margin you need to cover the shipping fees. How to Offer Flat Rate Shipping for Your Small Business Small businesses can offer flat rate shipping by charging the same fee for all orders regardless of their weight and size. Like free shipping, flat rate shipping eliminates surprises. Choosing a flat rate shipping fee that allows you to break even can be challenging. Flat rate shipping is most viable for businesses whose products fall within a similar weight and size range. For example, if you operate a coffee roastery and can predetermine how much it costs to ship your bags of beans or coffee subscription service, flat rate shipping could be perfect for you. However, if you sell handmade household goods ranging from teapots to tables, it will be difficult to produce a flat rate shipping fee. How to Offer Real-Time Shipping for Your Small Business You can offer real-time shipping for your small business by connecting customers to courier providers and showing them real-time shipping costs based on their order’s destination, volume, and weight. This puts the patron in the driver's seat. However, if the customer doesn’t like any of their options when they go to checkout, they’re more likely to abandon their cart. To avoid this, consider providing a matrix rate shipping calculator on your product page. A matrix rate shipping calculator lets the customer enter their location and then estimates their shipping expenses for them. Matrix Rate Shipping Equation: shipping cost x weight x cart value x destination = the matrix rate shipping fee How to Offer Same Day Delivery for Your Small Business Given the speedy shipping times of companies like Amazon, offering same-day shipping will help you compete with the industry's giants. While most major carriers provide local same-day delivery, you can also use third-party delivery services. Uber now offers Uber Direct, which employs its network of drivers to move goods from supply chain locations and deliver them to customers. Another great option is Roadie, a UPS company that uses a crowdsourced logistics platform that offers same-day delivery of any item to over 90% of American households. If you have a storefront, make same-day pickup free. Free in-store pickup attracts delivery-fee wary patrons and lures online customers into your business, often leading to additional sales. If most of your clients are local, staffing and training delivery drivers could be worthwhile. Consider setting up an in-house delivery service to avoid third-party fees or shipping expenses. How to Offer Drop Shipping for Your Small Business A drop shipping service provides warehouse access and manages inventory and fulfillment for you. It is an offhanded way for retailers to fill orders. Rather than manufacturing the products they sell, companies that use drop shipping send orders placed on their site to their network of suppliers. The supplier contacts the warehouse nearest the customer, and ships their order to them. If you produce your products, then drop shipping isn’t for you. Back to Top Best Shipping Company for Small Business There are many shipping companies to choose from, but what is the best shipping company for small businesses? Some shipping companies offer better shipping rates for small businesses than others. From the best-known shipping companies to smaller providers, we explore popular shipping services and what they offer to small businesses below. USPS Small Business Shipping USPS shipping rates for small businesses are discounted, and they also offer loyalty credits to small businesses. If you operate a cottage food business, the home pickup service USPS provides makes them a convenient choice for small businesses that ship from home. Free API so you can integrate shipping tools to your website Home pickup Loyalty credits Volume-based discounts Free package pickups Direct mail marketing and advertising assistance 2-8-day average delivery timeline FedEx Small Business Shipping If you're looking for a fast-shipping option, then FedEx is perfect for your small business shipping needs. FexEx makes standard home deliveries on both weekdays and weekends, increasing their shipping delivery time by two days compared to other popular carriers. Weekend deliveries An e-commerce center that aids in online business development Annual small business grants Administrative support Educational blog and podcast Shipping cost calculator Ground transit map Custom boxes and inserts UPS Small Business Shipping UPS is ideal for small businesses that ship large packages. Their large flat rate box shipping price begins at just $18.40. UPS offers discounted shipping rates for small businesses as well. Large flat rate boxes start as low as $18.40 Their eFulfillment portal provides a cloud-based tool that helps you store and ship products across multiple platforms Discounts for small businesses Tracks and manages shipping expenses Overnight, international, same day, and group shipping options Sendle Small Business Shipping Sendle is the ideal shipping service for small businesses that are shipping packages under 20 lb. Discover the benefits of shipping with Sendle below: Will beat the price charged by major carriers on domestic packages up to 20 lb. Carbon neutral shipping Zero contracts or subscription fees Certified B corporation DHL Express Small Business Shipping If your small business is filling international orders, consider shipping with DHL Express. They provide a wealth of resources for small businesses to help them enter the global marketplace. Expertise with international shipping Transparency of service/rate fees Provides resources that help small businesses navigate international shipping ShipBob Small Business Shipping As a third-party logistics company (3PL), ShipBob is a great shipping service for exclusive e-commerce businesses. Discover the benefits of using ShipBob below: Bulk shipping discount rates Warehousing and inventory management EasyPost Small Business Shipping EasyPost helps you secure the best shipping price for your small business by connecting you to multiple carriers and comparing their rates. API is free for up to 120,000 shipments a year Shows the prices of over 100 carriers Simplifies, automates, and controls the shipping process Data-backed optimization Label creation tool Real-time shipping updates What Is 3PL? A 3PL provider works in supply chain management to store, package, or transport goods. Each third-party logistics provider will offer a unique range of services, so read the contracts carefully before selecting a 3PL provider. In most cases, companies integrate their 3PL provider into their warehousing process and outsource their shipping operation to their 3PL. Benefits of 3PL Working with a 3PL outsources your warehousing and shipping process so you can invest in other aspects of your business. Pay the 3PL to store your inventory and then pick, pack, and ship your orders as they’re received. All you have to do is ship your stock to their warehouse and sync your e-commerce orders with their inventory. Each 3PL service will vary, but many allow you to choose between paying them a monthly fee or per order (depending on the services you've chosen). If your operation is still burgeoning, these fees will offset the benefits of using a fulfillment and warehousing service. However, if you're filling more orders than you can store and send yourself, it’s time to hire a 3PL service. 3PL Pros and Cons: As your e-commerce business grows, use our 3PL pros and cons list to decide if working with a third-party logistics provider would benefit your business: Reduced Shipping Costs - Fulfillment warehouses secure a reduced bulk shipping rate. Most offer e-commerce shipping integration across the major shipping logistics and third-party logistics channels. Get Products to Customers Faster - Shorten your shipping times by analyzing your data and choosing a 3PL partner with warehouses near your target customers. Service Fees - You’ll have to pay your 3PL for storing, picking, packing, and shipping your products. Generic Unboxing - You surrender control of how your products are packaged and presented, which eliminates thoughtful unboxing experiences. Back to Top Types of Packaging Materials for Shipping The products your small business sells determine the shipping packaging materials you need. Foremost, you must choose a vessel to contain your product. Fragile merchandise requires padding, perishables demand cooling packs, and heat-sensitive items need insulation. We break down the top three types of packaging materials for shipping below, so you can make an informed shipping packaging purchase. Weather-Resistant Poly Mailers - Poly mailers are made from polyethylene film (plastic). They’re durable, lightweight, and weatherproof, but they don’t cushion your products. Poly Mailers are the best shipping packaging for tea, coffee, clothing, and other malleable items. Padded Mailers/Bubble Mailers - Padded mailers are lightweight, which lowers your shipping expenses. Their cushioning helps protect delicate items during transit, but they’re not weather resistant. Padded mailers are the best shipping packaging for books, jewelry, and small electronics. Shipping Boxes - Shipping boxes are the best way to protect your products and create an unboxing experience. You can curate the layout of your merchandise inside your shipping box and add additional promo items. Shipping boxes are heavier than both padded mailers and poly mailers, making them more expensive to ship. Shipping boxes are the best shipping packaging for subscription boxes, large items, products that require cooling packs, or any small business that wants to create an unboxing experience. Back to Top How to Calculate Shipping Costs for Small Business To calculate shipping costs for your small business, you must consider five factors: speed, shipping packaging, weight + dimensions, destination, and shipping frequency. We break down each of these five factors below, so you have the tools you need to calculate your small business shipping costs: Speed - Most customers expect fast and free shipping. Depending on the size of your company and the products you sell, fast and free may be impossible. Evaluate the different carrier options and decide whether the fastest shipping choice is in your budget. Shipping Packaging - From the cushioning material to the container, you must purchase packaging. As a small business, you use shipping packaging to curate a branded unboxing experience that includes pops of color, logo stickers, handwritten notes, etc. Weight + Dimensions - All carriers will charge by the weight of the package. Many carriers also account for the dimensional weight (DIM) and increase fees for packages that take up a lot of space. Destination - The farther your package travels, the greater the fee. Carriers calculate distance pricing based on how many shipping zones your package must travel through. Additionally, shipping to a commercial property often costs more than shipping to a residential location. Shipping Frequency - If you use their shipping services often, many carriers will offer you a discount. What Is a Shipping Zone? Shipping zones, also known as postal zones, are predetermined geographical areas shipping companies use to measure how far a package traveled. Rather than calculating miles, shipping zones determine distance by grouping ZIP codes along the route. Shipping carriers base their distance pricing on how many shipping zones the package traveled through to reach its destination. Domestic shipments in the US go from Zone 1 to Zone 8. Scale your operation with our shipping tips for small businesses. Your shipping strategy isn’t just essential for getting products to customers, it’s an integral part of how you do business. The shipping method you choose needs to be affordable, and it also needs to be transparent. Reference our guide to small business shipping solutions anytime you have a shipping-related question.