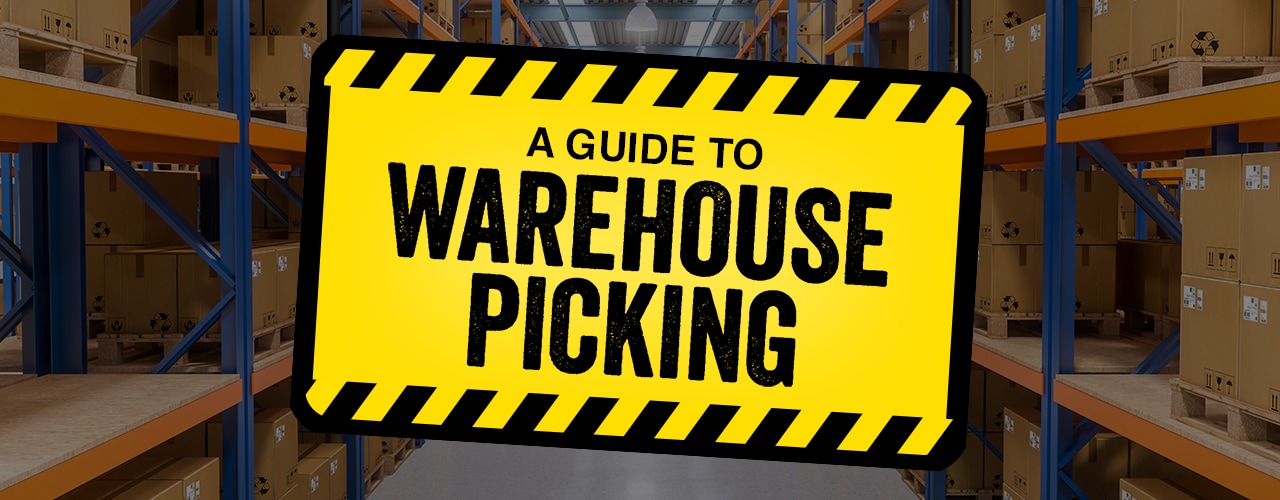
Order Picking in a Warehouse
Last updated on 2/8/2023Order picking is the first step in the fulfillment process for an ecommerce business or distribution center. When an order is placed with your company, the items must be “picked” from your storage area. The type of order picking that you implement heavily influences the organization and layout of your warehouse. Picking is also one of the most expensive processes in warehouse operations, which means it should be planned out with care. Keep reading to learn about order picking and how to incorporate different picking strategies.
Shop Order Picking CartsWhat Is Order Picking?
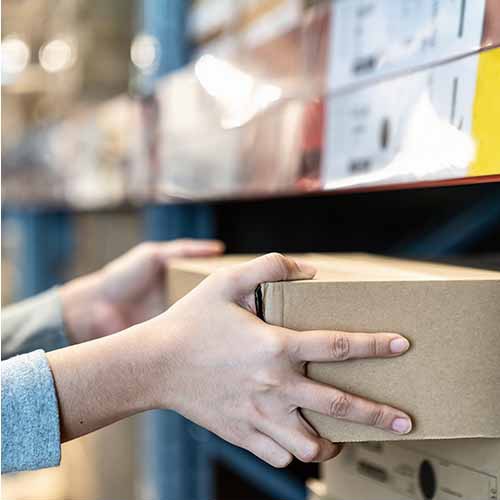
Order picking is the process of pulling items from storage areas to fulfill customer orders. This is a manual process that requires order pickers to physically locate items and pull them from shelves. It sounds easy, but there are many considerations to keep in mind. How do order pickers find the items? In what order should items be picked? If you don’t create an organized picking strategy from the start, the process has the potential to become chaotic and inefficient. Thankfully, there are several established methods of order picking that will help you streamline your operations.
How Does Order Picking Work?
Order picking is a little bit like shopping at the grocery store. You start with a list, and you locate each aisle to find the items you need. Pickers even use shopping carts to collect items in some warehouses! At the start of the shift, each picker is given a list of items categorized by SKU, location, or order invoice. They travel around the warehouse to each storage location, retrieve the items they need, and place them in their cart or basket. When their assignment is complete, they transfer items to the packing station and shipping zone and start their next assignment.
What makes a good order picker? Remember that you are relying on the order picker to find the right items promptly while dodging the many obstacles in a warehouse. These are some qualities to look for in a successful order picker:
- Urgency - Order picking is a fast-paced warehouse job that relies on individuals to navigate the building quickly while remaining aware of forklifts and other material handling equipment.
- Attention to Detail - A good order picker reads their assignments carefully and matches up the SKUs on their list. They also need to be on the lookout for damaged merchandise or items placed in the wrong locations. This is often how customer orders are fulfilled incorrectly. An item of a different color or size is placed in the wrong storage location and pulled by the picker.
- Good Sense of Direction - A large fulfillment center can seem like a maze. The best order pickers know their way around the many aisles and have memorized the quickest routes to each location. The key is to take as few steps as possible to get the job done.
Types of Order Picking
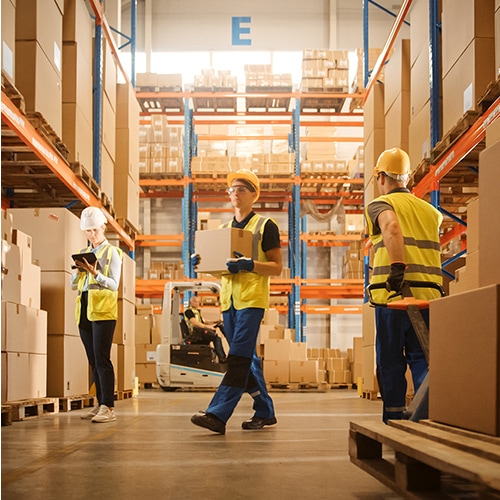
Different types of warehouses require different order-picking solutions. When you choose a process for your business, take into consideration your resources, warehouse layout, and the types of items you sell. Check out the most popular ordering picking systems below:
1. Discrete Picking
Ideal for smaller warehouses, discrete picking is easy to understand and implement. Order pickers complete one customer order at a time, locating each item in the warehouse until the order is complete. This requires the picker to travel from location to location, which can be time-consuming in a larger warehouse. For small businesses with less inventory, it’s a great way to keep track of each order.
- Best for: Small warehouses with less inventory
- Worst for: High-volume warehouses with large floor plans and complex orders
2. Zone Picking
In zone picking, instead of sending out the pickers to search the whole warehouse, each picker is assigned to a zone. The zone is a defined space within the warehouse storage area. The pickers work in their zone only, retrieving items for customer orders. Any time an order is received that contains items from their zone, they are provided with a list to work through. Zone picking is better for larger warehouses because the pickers don’t have to travel long distances, they just stay in their assigned zone.
- Best for: Large high-volume warehouses
- Worst for: Small warehouses with limited inventory
3. Batch Picking
Batch picking is similar to discrete picking, but instead of working on one order at a time, pickers work on several orders simultaneously. This sounds confusing, but the benefit is that the picker can pull multiple items based on their location. For example, if three orders contain the same item, the picker can pull them all at the same time. This would be three trips to the same location with discrete picking. With batch picking, the extra trips are eliminated. The downside to this type of picking is that orders can become mixed up, but it can be very successful with efficient, highly-trained order pickers.
- Best for: High-volume orders that contain many of the same items
- Worst for: Complex orders that contain many different items
4. Wave Picking
Wave picking is unique because it’s based on timing. A warehouse management system analyzes shipping schedules to prioritize orders that have the same carriers and shipping times. Orders that need to ship first are picked first, instead of orders being picked as they are received. Pickers are assigned to picking periods, or waves, that only last a predetermined length of time. They don't pick continuously throughout the shift, which helps cut down on fatigue. Once the wave is over, pickers perform other tasks until the next wave.
- Best for: Reducing downtime between orders and travel time between picking locations
- Worst for: Warehouses that process orders as soon as they are received
How to Organize Picked Items
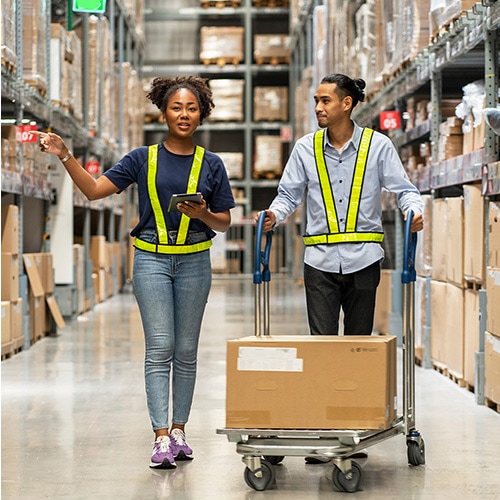
Order pickers only have two hands, so they need to rely on different methods to collect orders. These are the most common ways to organize picked items for shipping:
- Piece Picking - In piece picking, each item in the order is picked one at a time. Individual items can be collected in a shopping cart or shopping basket. This method works for small items that can be carried by hand.
- Pallet Picking - Pallet picking involves picking an entire pallet stacked with goods and transferring it to the shipping area. This type of picking requires the operation of a pallet jack.
- Case Picking - Instead of picking individual items, sometimes pickers need to pull a whole case. Case picking occurs when full cases are loaded onto a dolly or cart.
Automated Picking
Automated picking might sound futuristic, but it's not just related to robots. Many automated processes are probably already familiar to you. Introducing automated systems helps to improve accuracy and reduce picking times.
- Tablets - Picklists used to be printed on paper, but now many warehouses utilize digital tablets that automatically update with new assignments for order pickers.
- Scanners - Mobile scanners can be synced with your inventory management system to simplify the picking process. The scanner reads barcodes to ensure the picker has selected the right items, but it can do much more. Barcode-picking technology can be set up to create picking lists, prioritize items, and even direct pickers where to go.
- Voice Picking - Order pickers wear headsets that give voice commands directing them where to locate items and what to pick.
- Robotic Picking - A solution to staffing shortages, AI-powered robots are capable of picking orders with speed and accuracy.
Picking Best Practices
While order picking does rely on individual employees to pull the right items, there are practices you can put into place to help your team.
- Good Lighting - In a large warehouse there are always far-off locations that don't have proper lighting. This makes it difficult for order pickers to find items and read barcodes. Keep your aisles and racking systems well-lit with industrial lighting fixtures to promote accuracy.
- Correct Bin Labeling - Before order pickers can do their job, you need to have an organized system for storing goods. Bins, pallet locations, and racking systems should be clearly labeled.
- Floor and Zone Markings - Use floor labeling to direct your warehouse traffic and alert employees to hazards.
- Ladder Safety - If you rely on vertical space to store items, make sure your order pickers are educated on the safe use of ladders to pull items.
Order picking is a process that accounts for a large portion of your operating costs. Invest careful planning into the types of picking systems used in your warehouse to help improve your bottom line. Use our order-picking guide to familiarize yourself with best practices and established methods.